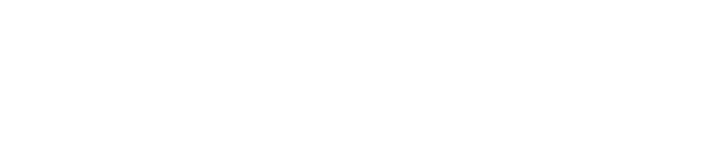

XL Star Type Spider Jaw Coupling Flexible Shaft Coupling Rubber Coupling Spider Industrial Flexible Curved Jaw Coupling

A rigid coupling is a mechanical component that connects two shafts within a motor or mechanical system. It can be employed to link disparate systems, such as coupling a motor with a generator, or to mend a connection within a singular system. A rigid shaft coupling is designed to be inflexible, ensuring exact alignment and a firm grip.
The assortment of rigid coupling types encompasses flange coupling, sleeve coupling, and clamp or split-muff coupling. Each variant primarily aligns and secures two shafts to transmit power with efficiency. The rigid flange coupling is notably favored for its straightforward installation and sustained alignment capabilities. Flange couplings are robust and frequently employed in heavy-duty settings. Sleeve couplings, with their simpler construction, are apt for confined spaces. Clamp or split-muff couplings are valued for their ease of assembly and disassembly, which is advantageous for maintenance without the need to dismantle the entire system. Other specialized forms, such as rigid compression coupling and grc coupling, cater to specific needs that demand extra clamping force or compatibility with particular pipe types.
The architecture of a rigid coupling typically involves two flanges that are permanently affixed to the respective shaft ends. These flanges are then securely bolted together. For a rigid flange coupling, each flange is attached to a shaft, and the pair is joined using bolts or nuts. This design's simplicity translates to minimal upkeep and a dependable connection capable of withstanding significant torque and axial forces. Certain rigid couplings, such as the victaulic 107n and 009n victaulic, feature unique grooved configurations that facilitate a more efficient installation while maintaining a strong and secure bond.
Constructed from diverse materials like aluminum alloy, cast iron, stainless steel, zinc, carbon steel, and alloy steel, rigid couplings cater to various applications. Aluminum alloys, being lightweight and corrosion-resistant, are well-suited for aerospace and automotive uses. Cast iron, known for its tensile strength and resilience, is ideal for industrial applications. Stainless steel, prized for its robustness and corrosion resistance, is essential in marine and chemical processing. Material selection is pivotal for the coupling's efficacy and durability, with each offering unique advantages for specific uses. For instance, zinc and carbon steel are chosen for their affordability and strength, while alloy steel is preferred in scenarios demanding exceptional toughness and resistance to wear.
In various industries, particularly where exact shaft alignment is critical, rigid couplings are indispensable. Manufacturing facilities utilize them in conveyor systems, mixers, and extruders. Machinery repair shops leverage rigid couplings to restore equipment to peak condition. In construction, they are integral to heavy machinery, ensuring consistent power transmission. The dependability of rigid couplings in preserving alignment and power transfer is invaluable in environments where downtime equates to substantial economic loss. Moreover, in the automation sector, rigid couplings are crucial for precision in motion control systems, which is imperative for producing high-caliber goods.
The fundamental role of a rigid coupling is to unite two aligned shafts and facilitate torque transmission from one to the other, ensuring synchronized rotation and power. In contrast to flexible flange coupling, a rigid coupling does not tolerate misalignment or axial movement, rendering it suitable for scenarios where shaft alignment is consistent and foreseeable. This is especially relevant in power generation, where precise alignment is essential for the efficient conveyance of energy from turbines to generators.
Characterized by their simplicity and robustness, rigid couplings lack moving parts, which diminishes the likelihood of malfunction, thus offering a dependable option for essential applications. Some rigid couplings boast a protected flange coupling design, incorporating shields to safeguard the bolts from environmental hazards, thereby enhancing their longevity. Models like the victaulic 107n and victaulic 009n introduce innovative grooved technology that expedites installation without sacrificing strength. Their key selling points include the ease of installation, which can substantially minimize downtime during maintenance or reconfiguration.
Employing a rigid coupling yields numerous advantages, such as sustained precise shaft alignment, pivotal for machinery's smooth functioning. This accuracy curtails vibration and noise, contributing to a longer service life for the equipment. The sturdy construction of rigid couplings, exemplified by the 1 rigid coupling or the 2 1 2 rigid coupling, enables them to endure high torque demands, making them apt for heavy-duty tasks. The positive impacts of utilizing rigid couplings include enhanced system dependability, diminished maintenance expenditure, and heightened operational efficiency.
A rigid coupling is a fixed apparatus that secures two shafts in place, disallowing any flexibility, whereas a flexible coupling can accommodate shaft misalignment and movement. The decision between a rigid and flexible coupling hinges on the specific needs of the application, such as the requirement for precision alignment or the capacity to absorb shocks and vibrations.
In the selection of a rigid coupling, it is crucial to consider factors like torque capacity, shaft dimensions, and alignment potential. The operating environment is also a determinant in choosing the appropriate material and coupling type. Moreover, the nature of the load—constant or variable, the presence of axial or radial forces, and the need for torsional rigidity—should guide the selection process.
To guarantee the extended lifespan of a rigid coupling, regular maintenance is essential. This entails inspecting for corrosion, verifying that bolts are tightened to the proper specifications, and monitoring for wear. Correct installation and alignment from the start are also vital to avert premature deterioration. Where applicable, consistent lubrication and routine inspections can aid in detecting issues before they escalate to system failure.