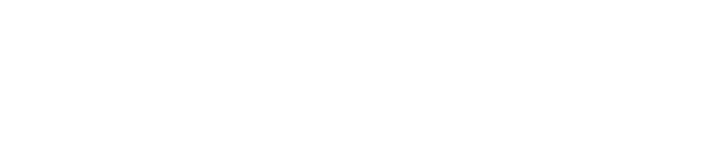

Factory Directly Refractory Material Sepiolite Price Powder Meerschaum Sepiolite Powder Fiber For Coating

Refractory materials are specialized substances that exhibit properties of extreme heat resistance, often used in environments where high temperatures are a common occurrence. These materials are crucial in industries such as steelmaking, metallurgy, glass manufacturing, and petrochemical production, where the ability to withstand intense heat is a fundamental requirement. The cost of refractory materials can vary significantly based on their composition and the manufacturing processes involved in their production.
The primary function of refractory materials is to provide a lining for furnaces, kilns, and other thermal containment systems. The effectiveness of a refractory lining depends on its ability to resist thermal shock and chemical corrosion, as well as its structural integrity at high temperatures. To achieve this, refractory materials are designed to maintain their shape and strength under extreme conditions. They must also insulate the heat generated within the furnace to ensure that it does not escape into the surrounding area.
Businesses that operate in sectors requiring high-temperature operations must carefully select the type of refractory material that aligns with their specific needs. The choice of refractory material will impact the performance and longevity of their thermal processes. Therefore, understanding the cost associated with these materials is essential for strategic decision-making in industrial settings.
Refractory materials are diverse and can be tailored to specific applications based on their composition and properties. Some common types include:
Alumina Refractories: Made primarily from alumina (Al2O3), these refractories are used in a wide range of applications due to their high purity and excellent resistance to corrosion. They are commonly found in industries such as cement production and glass manufacturing.
Zirconia Refractories: These refractories contain a high percentage of zirconium dioxide (ZrO2) which provides them with exceptional mechanical strength at high temperatures. Zirconia refractories are often chosen for use in high-stress environments like steel production.
Silica Refractories: Composed of high-purity silica (SiO2), these refractories are known for their excellent thermal shock resistance and high melting point. They are frequently used in critical areas of glass furnaces and can handle extremely high temperatures.
Magnesia-based Refractories: These are made from magnesium oxide (MgO) and offer good resistance to basic substances. They are suitable for lining basic oxygen converters (BOCs) in steel production and are also used in non-ferrous metal applications.
Carbon-based Refractories: Made from carbon or graphite, these refractories are electrically conductive, making them ideal for certain applications such as electric arc furnaces in steel production.
Each type of refractory material has specific properties that make it suitable for particular uses. For instance, alumina refractories are favored in cement kilns and glass tanks because of their ability to resist fluxes and other materials at high temperatures.
When selecting refractory materials for business needs, it is important to consider several factors impacting material cost and performance. The choice of material should align with the specific application's demands in terms of temperature resistance, mechanical strength, chemical composition, and environmental conditions.
For instance, if the application involves exposure to high-temperature environments where thermal shock is a concern, choosing a material with superior resistance to rapid temperature changes like silicon carbide or fused cast refractories may be prudent. On the other hand, if the material will be subjected to chemical corrosion, selecting an appropriate chemical composition such as high-alumina or magnesia-chrome may be necessary.
Additionally, the geometry of the structure being lined is a crucial consideration. Complex shapes may require custom-shaped refractories that can be more costly than standard blocks or mixes. The installation process should also be factored in; some materials may require specialized equipment or expertise for handling delicate or large-scale installations.
Businesses should also account for supplier reliability when purchasing these materials on a B2B platform like Alibaba.com. It is essential to choose suppliers who can provide consistent product quality and support—factors that can significantly impact material performance and longevity in industrial settings.
Alibaba.com stands out as a comprehensive marketplace where businesses can source a wide array of refractory materials suited for diverse industrial needs. With an expansive network connecting buyers with suppliers globally since 1999, Alibaba.com offers an impressive selection that caters not only to large-scale operations but also niche industries requiring specialized materials. The platform simplifies international trade by providing tools that facilitate easy communication between buyers and sellers in local languages and mobile-friendly features ensuring that transactions can be conducted effortlessly on-the-go.
The diversity of materials available on Alibaba.com includes options such as fused cast AZS (alumina-zirconia-silica) bricks for high-temperature applications, calcium silicate boards for fire protection in buildings, and ceramic fibers for insulation in kilns and furnaces. Moreover, Alibaba.com's Trade Assurance service provides an added layer of security by protecting payments until delivery is confirmed complete.
With its commitment to helping small and medium-sized businesses thrive by providing global trade solutions that simplify sourcing industrial products without compromising quality, Alibaba.com has become a trusted partner for many companies worldwide. The platform's extensive range of refractory materials ensures that whether you're in metallurgy or manufacturing, finding suitable products for your business needs is not only possible but also an efficient and user-friendly experience.
Refractory materials are utilized in various industrial applications that require resistance to high temperatures, such as in furnaces, kilns, and ovens for the production of materials like steel, cement, and glass.
Refractory materials are designed to withstand high temperatures without deforming or melting, ensuring the structural integrity of the insulated system they are used in.
The main raw materials for refractory materials include alumina, silica, zirconium, and magnesia, depending on the required properties of the refractory product.
When choosing a refractory material, consider factors such as the maximum service temperature, chemical resistance needs, mechanical strength, thermal conductivity, and insulating properties.
The chemical composition of a refractory material determines its resistance to different environments and chemical reactions, making them suitable for specific industrial processes where chemical stability is crucial.
Yes, refractory materials can be customized with different types of aggregates or additives to meet the specific requirements of an industrial application.
Thermal conductivity is crucial in applications where heat transfer is necessary, such as in furnaces, boilers, and kilns, allowing these materials to maintain their structural integrity and performance.
The density of a refractory material impacts its resistance to thermal shock, strength-to-weight ratio, and thermal insulation properties, which are essential factors in various industrial applications.
Refractoriness is the ability of a material to withstand high temperatures without deforming or softening, which is crucial for maintaining structural integrity in refractory-lined furnaces or kilns.
Environmental factors such as temperature fluctuations, chemical exposure, and mechanical stress can affect the performance of refractory materials. It is important to select a material that is designed to withstand the specific conditions of your application.
Alumina-based refractory materials are commonly used in applications that require excellent thermal stability and resistance to wear, such as in metal processing and high-temperature manufacturing processes.
The quantity of refractory material needed will depend on the size of the area to be lined, the thickness required for insulation or protection, and the shape of the structure being lined.
Many refractory materials can be recycled due to their composition. However, the specific recycling options will depend on factors such as the material's purity, chemical composition, and structural integrity.
Considerations for installation include the chosen method (e.g., casting or gunning), the surface preparation of the substrate, and the curing process for castables. Proper installation is essential for optimal performance and durability.
Regular inspections and timely repairs or replacements can help maintain the longevity of refractory materials. Proper storage and handling are also important to prevent damage or degradation.