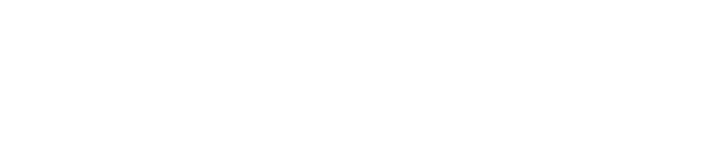
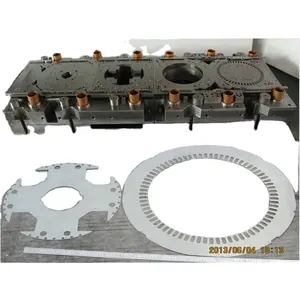
Mould Metal Punching Mould Die Progressive Stamping Die Custom Stamping Mold Progressive Stamping Die
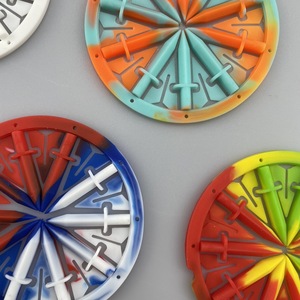
Moulds Mould Injection Plastic Mold Molding Custom Die Moulds Plastic Mould For Other Plastic Products


Moulds, in the context of manufacturing and industrial applications, are essential tools used for shaping materials into precise forms. They work on the principle of casting, where a liquid or malleable substance is poured or injected into the mould and then allowed to solidify, taking on the desired shape. Moulds are crafted to meet exact specifications and can be used to produce a wide array of items, from simple household products to complex machinery components.
Moulds are designed for a variety of users including manufacturers, artisans, and builders. They serve multiple industries such as automotive, aerospace, construction, consumer goods, and healthcare. The design of a mould is critical; it must not only correspond to the part's dimensions but also take into account the material's properties, the manufacturing process, and the intended application of the final product.
The manufacturing process employing moulds can be automated for mass production or customized for bespoke items. Mould-making materials must be chosen based on their compatibility with the substance being molded and the required durability of the mould itself. For instance, steel moulds are used for large production runs due to their longevity, while silicone or rubber moulds might be selected for intricate designs requiring flexibility.
In the world of fabrication services, there are several types of moulds available that cater to different needs and applications:
Injection Moulds: These are used in injection molding processes where molten material is injected under high pressure into a mould cavity. Injection moulds are commonly used for producing plastic parts in large volumes due to their ability to produce complex shapes with high precision.
Blow Moulds: Utilized in blow molding operations, these moulds are designed to form hollow plastic parts such as bottles and containers. The process involves inflating a heated plastic tube until it fills the mould and takes its shape.
Compression Moulds: These types of moulds are employed in compression molding where a preheated material is placed into an open mould cavity and then closed under pressure. This method is often used for thermosetting plastics and rubber.
Rotational Moulds: Rotational molding involves a heated hollow mould which is filled with a charge or shot weight of material. It is then slowly rotated causing the softened material to disperse and stick to the walls of the mould. This technique is often used for large hollow pieces such as tanks and playground equipment.
Extrusion Moulds: In extrusion molding, material is forced through a die that shapes it into a continuous profile. Extrusion moulds are used for creating pipes, tubes, and profiles with a uniform cross-section.
Selecting the right mould for your business hinges on understanding your specific manufacturing needs and the characteristics of your product. Here’s what to consider:
Material compatibility is paramount; ensure that the mould material can withstand repeated exposure to the substances you'll be working with without degrading. For instance, high-temperature resins require heat-resistant mould materials like steel or certain alloys.
Consider the volume of production. High-volume runs may justify investing in more durable metal moulds that can withstand wear and tear over time, while lower-volume or prototype productions might use less expensive silicone or 3D-printed moulds.
The complexity of your product’s design also plays a significant role. More intricate designs may need advanced moulds with fine details or multiple parts that can come apart to release the final product without causing damage.
Lastly, factor in potential future changes in design or material that could make your current choice of mould obsolete. Opting for adaptable or modifiable mould systems could save costs in long-term scenarios where product iterations are anticipated.
Alibaba.com stands as an expansive marketplace connecting businesses with an extensive range of wholesale mould suppliers from around the globe. The platform offers an extensive selection suited for various industries including automotive, construction, consumer goods, and many more. With filters tailored to specific needs like application area, color options, surface treatments, runner types, and material choices, Alibaba.com simplifies the search for appropriate mould solutions.
Partnering with Alibaba.com means businesses can collaborate with suppliers to customize their orders based on their unique requirements ensuring that every aspect from design style to functionality aligns with their project goals. Furthermore, through services such as Trade Assurance, Alibaba.com provides peace of mind by securing payments until delivery completion.
Choosing Alibaba.com allows businesses not only access to diverse product options but also leverages Alibaba's global reach ensuring that no matter where you operate from or what your industry specialization may be, you have access to resources that can help scale your production effectively while maintaining quality standards.
Materials used for mould manufacturing depend on the production requirements and can range from metals like steel and aluminum for durability to silicone and rubber for flexibility and intricate details.
Selecting the right type of mould involves evaluating factors such as material compatibility, production volume, product design complexity, and the potential need for future adaptability.
Hot runners keep the plastic material molten throughout the injection process, reducing waste and cycle times, while cold runners allow the material to cool and solidify, which may require additional steps to remove the runners.
Yes, moulds can be customized to meet specific design requirements, including unique shapes, sizes, and surface finishes.
When choosing a mould supplier, consider their expertise, production capabilities, quality assurance processes, communication efficiency, and ability to meet deadlines.
To ensure longevity, maintain your moulds properly with regular cleaning, lubrication, and inspections for wear and damage. Also, use the correct materials and process parameters during production.
Yes, there are eco-friendly options such as biodegradable materials and energy-efficient manufacturing processes that reduce environmental impact.
Lead times for custom moulds can vary greatly depending on the complexity of the design and the manufacturer's current workload but generally range from a few weeks to several months.
Surface treatments can enhance a mould's performance by improving wear resistance, minimizing friction, and ensuring easy release of the finished product.
After-sale services may include onsite installation, inspection, training, return and replacement policies, and provision of free spare parts.