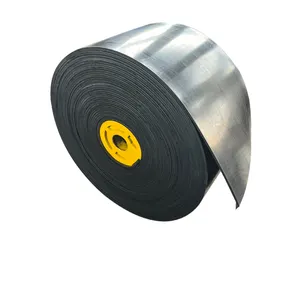
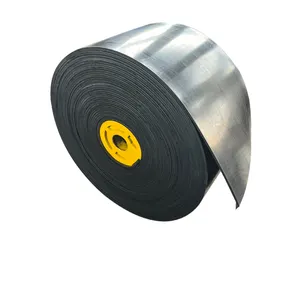
The conveyor belt industry, a cornerstone of numerous sectors such as logistics, mining, and manufacturing, is undergoing a significant transformation. With the rubber conveyor belt market projected to grow at a CAGR of 4.02% from 2023 to 2028, the industry is becoming increasingly competitive and dynamic. However, it also faces several challenges, including operational issues and environmental impact. This article delves into the current state of the conveyor belt industry, the challenges it faces, and the innovative solutions that are revolutionizing it. We will explore the advancements in materials and technology, and how they are shaping the future of conveyor belt rubber.
The Rubber Conveyor Belt Market is witnessing significant growth, with a projected CAGR of 4.02% from 2023 to 2028. This growth is driven by increasing demand from various industries such as logistics, mining, manufacturing, and metal processing. Rubber conveyor belts, categorized as heat-resistant, oil-resistant, fire-resistant, and chemical-resistant, are becoming integral to these industries. The market landscape is also shaped by major acquisitions and mergers, indicating a competitive and dynamic industry.
Conveyor belts, especially those made of rubber, face numerous challenges in various industries. The most common issues include belt damage, often due to handling heavy or abrasive materials, and premature wear and tear. Belt slippage, typically around the head pulley, is another problem. Material carryback, where remnants are left on the belt post-discharge, can cause blockages and accelerate wear. Lastly, damaged or seized idlers, often a result of excess material on the belt, pose significant challenges. These issues can lead to operational downtime and productivity loss.
The manufacturing of industrial conveyor belts, primarily made of rubber, has a significant environmental impact. These belts, especially the multi-ply type, use a lot of energy and materials, contributing to a large carbon footprint. The raw materials, including polyester/nylon fabrics and synthetic rubber components, are derived from crude oil. Unfortunately, recycling these belts is challenging and less prevalent compared to other rubber products like car tyres. The industry's environmental impact is further exacerbated by the disposal of worn-out belts, which often end up in landfills.
Conveyor belt applications vary greatly, impacting belt life from a few weeks to over 10 years. The product conveyed and the operating environment significantly affect belt life. Conveyor design and maintenance are also crucial factors. There are hundreds of conveyor belt styles, each with unique qualities suited to different conveying applications. Proper tensioning and tracking during installation, along with the use of v-guides, can assist in steering the belt and extending its lifespan. Improper storage can lead to material camber, so belts should be stored off the floor in a dry area.
Innovations in conveyor belt technology have led to the development of advanced materials and intelligent monitoring systems. Advanced polymers, composites, and reinforced fabrics enhance conveyor belt performance and lifespan. Intelligent monitoring systems, utilizing sensors and IoT devices, allow for real-time data analysis, enabling proactive measures to prevent breakdowns and optimize performance. Automated maintenance systems and enhanced safety features have also been incorporated, improving safety and efficiency. These advancements in conveyor belt technology have revolutionized industries, enhancing safety, performance, and sustainability.
Rubber-based conveyor belts are widely used in industrial automation due to their versatility and excellent grip. Natural rubber, synthetic rubber, and blends are popular options in this category. They offer high abrasion resistance and flexibility and can handle a wide range of loads. Rubber belts are ideal for applications such as general conveying, package handling, and incline/decline transportation. Conveyor belt manufacturers are focusing on developing eco-friendly materials, such as recycled rubber or PVC materials with a reduced environmental footprint.
Predictive maintenance for conveyor belts is a significant technological advancement in manufacturing and maintenance. It uses real-time data, machine learning, and IoT technologies to predict potential equipment failures. By continuously monitoring parameters like temperature, vibration, and speed, it can detect early warning signs, reducing unscheduled downtime and ensuring smooth operations. This strategy allows industries to address maintenance needs during scheduled downtimes, leading to significant cost savings over time. The implementation involves integrating IoT devices, upskilling employees in data analysis, and collaborating with predictive maintenance experts.
The future of conveyor belt rubber is set to be shaped by significant changes. AI and Industry 4.0 technologies are revolutionizing conveyor systems, enhancing efficiency and predictive maintenance. Sustainability and eco-friendly practices will focus on energy efficiency and reduced environmental impact. Customization and modularity will cater to businesses' specific needs and future growth. As the conveyor industry embraces these changes, businesses will benefit from enhanced productivity, reduced costs, and a greener approach to material handling.
One leading company has introduced a sustainable conveyor belt made from renewable, biodegradable materials. This innovation reduces power consumption and ecological footprints, aligning with sustainability concepts. This series is as efficient and durable as conventional, synthetic belts. A patented special coating can achieve energy savings of up to 40%. These belts are suitable for various industries, including logistics, airports, and automotive manufacturing. After its lifecycle, the belt is biodegradable, adhering to a cradle-to-cradle model, promoting an enduring, eco-friendly cycle.
The future of conveyor belts lies in the integration of IoT solutions. IoT-enabled real-time alerts can prevent belt slippage, while IoT-based smart cameras can prevent material spillage. Real-time monitoring of seized rollers and automated cleaning can prevent blockages. Furthermore, IoT-based predictive maintenance can prevent belt mistracking. These advancements in technology not only improve the efficiency of conveyor belts but also significantly reduce downtime and maintenance costs.
The future of the conveyor belt industry is set to be revolutionized by significant changes. The integration of AI and Industry 4.0 technologies is enhancing efficiency and predictive maintenance, while a focus on sustainability is leading to energy-efficient and eco-friendly practices. Innovations like the sustainable conveyor belt, made from renewable, biodegradable materials, and the integration of IoT solutions are paving the way for a more efficient and sustainable conveyor belt industry. As the industry embraces these changes, businesses stand to benefit from enhanced productivity, reduced costs, and a greener approach to material handling. The conveyor belt industry is indeed on the cusp of a new era, driven by innovation and sustainability.