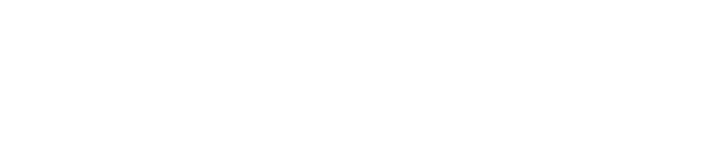
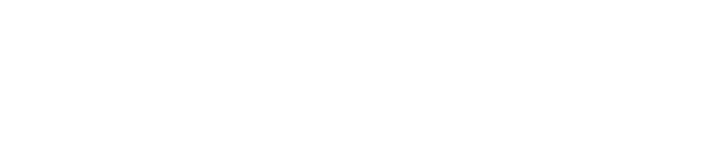
A CNC fixture plate, essential in the realm of machining, is a flat plate used as a base for securing, supporting, and positioning workpieces during CNC operations. These plates enhance precision and repeatability, which are crucial in manufacturing environments where consistency is key. This introduction delves into the various types and applications of CNC fixture plates.
The diversity of CNC fixture plates caters to different machining needs. A CNC mill fixture plate is designed to accommodate milling operations, providing a stable and precise base. For routing tasks, a CNC router fixture plate is tailored to ensure secure clamping and accuracy. The Tormach fixture plate is known for its modularity and ease of use, often used in smaller CNC mills for quick setup changes. In contrast, the CNC vacuum plate fixture uses vacuum technology to hold parts firmly in place during intricate machining tasks.
CNC fixture plates are not one-size-fits-all; they serve various applications. For instance, the Dayton CNC fixture plate is frequently employed in high-precision industries such as aerospace and automotive. The quick change fixture plate system is advantageous for operations requiring rapid turnover between production runs. Meanwhile, hobbyists and small-scale creators might opt for a Shapeoko fixture plate, which is compatible with Shapeoko CNC machines, known for their accessibility and ease of use.
Fixture plates are crafted from materials that ensure durability and stability. The choice of material impacts the plate's performance and longevity. Common materials include aluminum for its lightweight properties and steel for its robustness. The use of a fixture plate in CNC machining brings several advantages, such as reduced setup time, improved workpiece stability, and enhanced precision.
Selecting the appropriate fixture plate requires understanding the specific needs of the machining process. Factors to consider include the type of machine, the size of the workpiece, and the nature of the machining operation. It is crucial to match the fixture plate with the machine's capabilities, whether it's a standard CNC machine or a specialized one like a SMW fixture plate designed for particular models.
Incorporating a CNC fixture plate into the machining process can significantly enhance operational efficiency. Machinists and engineers must consider the compatibility of the fixture plate with their existing setup to ensure seamless integration. The right fixture plate can lead to a streamlined workflow, resulting in a more efficient production process.