
Pu coated bearing nylon pulley rubber omnidirectional wheel silicone roller customized unpowered polyurethane roller roller
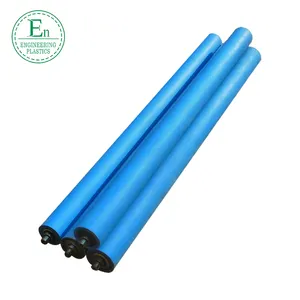
In the world of manufacturing, efficiency and cost-effectiveness are paramount. One key component that significantly influences these factors is often overlooked - the humble rubber roller. These rollers play a pivotal role in various industries, enhancing production capacity and reducing component failure. This article delves into the role of rubber rollers in production lines, their impact on efficiency, their types and specific uses, and the long-term cost benefits they offer. We will also explore real-life case studies demonstrating their transformative power and provide guidance on choosing the right rubber rollers for your production line.
Rubber rollers play a crucial role in various applications and industries. They offer services such as rubber roller recoating, resurfacing, recovering, reconditioning, and replacement. These services ensure the rollers' longevity and optimal performance in production lines. Contact our team on Alibaba.com to learn more about our high-quality rubber roller services.
Rubber rollers significantly enhance production capacity in manufacturing processes. Their resilience against stress, strain, and varying working conditions reduces component failure, allowing machines to operate continuously across different shifts. This competitive advantage makes rubber rollers a top ROI generator for firms. Moreover, the rubber materials used in the fabrication of the roller's outer surface outperform expectations, irrespective of the working conditions they are subjected to. Therefore, high-quality rubber rollers are crucial for efficient and uninterrupted production.
Rubber rollers, found in various manufacturing processes, are primarily used in the production of textiles, film, sheet, paper, and coiled metal. They are also essential in container and packaging fabricating equipment, and in machinery used for sanding and grinding wood, steel, and aluminum. Rubber rollers are typically cylindrical or spherical and are used in applications requiring high contact and holding friction. They are also used in printing, where hard rubber rollers ink the type before paper impression. Additionally, they are ideal for peripheral decorating of cylindrical shapes and roll-on decorating of large flat or curved surfaces.
Rubber Rollers greatly influence the costing decision made by manufacturers due to the capital investment in raw materials. They ensure a better quality of the processed fabric, lower the cost involved in electricity consumption by increasing productivity, and optimize the water consumption of the fabric production process. Producing fabric with a cost-effective technique like using Rubber Rollers is a solution to save more cost and increase the ROI.
In one case, a valve manufacturer faced frequent failures of a rubber seal in critical water cooling processes. The solution was a fully molded seal, produced using state-of-the-art compression vacuum presses. This resulted in a seal that didn't fail over 8 years of production. In another case, a supplier of replacement aircraft parts faced issues with an overseas rubber manufacturer. A new elastomer was developed to meet the exact compression/deflection characteristics required by the FAA, leading to a product that met all requirements. These cases highlight the transformative power of high-quality rubber products in production lines.
Choosing the right rubber rollers for your production line involves careful consideration of various factors. The type of rubber selected depends on the chemicals and solvents it will encounter during service. The rubber's ability to withstand working conditions such as load, shock, shearing, and abrasion is also crucial. Hardness and thickness of the coating are important criteria, with the hardness usually set between 30 and 85 Shore A, and the thickness between 10 and 35 mm. When several rubber materials meet the requirements, factors such as cost, life, grinding interval, and loss due to the exchange of rolls should be considered.
In conclusion, high-quality rubber rollers are an indispensable part of modern production lines. Their resilience, versatility, and cost-effectiveness make them a top choice for manufacturers across various industries. From textiles to aircraft parts, the use of rubber rollers has proven to significantly enhance efficiency and productivity, while reducing costs. The choice of the right rubber roller, considering factors such as chemical resistance, load-bearing capacity, hardness, and thickness, can make a significant difference in the overall performance of a production line. As demonstrated by the case studies, the transformative power of high-quality rubber rollers is undeniable. Therefore, investing in high-quality rubber rollers from reliable providers on Alibaba.com is a strategic decision that can revolutionize your production line.